Cogeneration systems-also called combined heat and power (CHP) systems—are designed to generate both heat and power. Jenbacher CHP systems use waste heat accrued during an engines operation to generate overall plant efficiencies of more than 90 percent. This efficient and economical method of energy conversion achieves primary energy savings of roughly 40 percent by using a gas engine cogeneration system instead of separate power and heat generation equipment. Transportation and distribution losses also are reduced or eliminated as the decentralized energy supply is aligned where it is needed.
How it works
The basic structure of Jenbacher CHP systems includes an engine/generator unit and heat exchangers that make use of waste heat. A wide range of heat sources—from engine cooling water and oil to an air/fuel gas mixture and exhaust gas—is configured to maximize the benefit to each individual customer.
Cogeneration systems can be supplemented with a boiler system for bridging peak heat demand periods. An increase in system operating time and efficiency is made possible by the connection of a heat storage medium.
Power plant electrical switch and control systems distribute electricity and manage the engine, while hydraulic equipment ensures heat distribution. Generated power is used by a facility or fed into the public power grid.
The thermal energy can be used to generate heating water and steam production as well as for various types of process heat.
Gas engine cogeneration systems also are used for CO2 fertilization in greenhouses and trigeneration systems (combined generation
Features & Benefits
» Cogeneration systems generate both heat and power
» Jenbacher CHP systems use waste heat from various sources to increase plant efficiency by up to 90 percent
» Cogeneration achieves 40 percent energy savings vs. separate power and heat generation equipment
» Reduces or eliminates transportation and distribution losses
» Addition of boiler system or other heat storage medium further increases operating time and efficiency
» Generated power is used by an individual facility or fed into a public power grid
» Thermal energy can be used to generate heating water and steam production, as well as for various types of process heat
» Cogeneration systems also can be used for CO2 fertilization in greenhouses and trigeneration systems.
CHP Delivers Stable Power Supply for Industry
Utilizing the local natural gas supply network gas engine-based cogeneration systems provide a stable supply of electrical power that, if needed, can be isolated from the local electricity grid. The heat produced by the engine can be recovered either as hot water or as steam for use in the industrial facility. In addition, if there is a local need for cooling power, the heat can be fed into an absorption chiller providing a source of cold water. This cold water can in turn be used to support a refrigeration or air conditioning system. Systems providing electricity, heat and cooling are called trigeneration plants. This can be taken one step further for industrial users that require carbon dioxide. Carbon dioxide can be recovered and scrubbed from the engine exhaust to the highest standards. There are various applications for this carbon dioxide including ones in the food and drinks industry or in greenhouses for the promotion of growth in plants.
CHP Improves Environmental Performance
Natural gas has the lowest levels of carbon dioxide production and is the cleanest of all the fossil fuels. Jenbacher gas engines generate electricity at high efficiency making the greatest use of the fuel source. The utilization of cogeneration for embedded generation helps minimize losses of electricity associated with its transmission from centralized power plants. With the addition of carbon dioxide recovery systems carbon dioxide can be sequestered in plants or utilized in manufacturing processes helping provide the highest levels of environmental performance.
CHP has Varied Industrial Applications
Cogeneration system systems can be successfully applied to a range of industrial applications including:
» Textiles
» Food processing
» Ceramics
» Construction
» Dyes & chemicals
» Mining
» Oil & gas
» Packaging
» Paper
» Pharmaceuticals
» Rubber
» Steel
To find out more about how gas engine based combined heat and power can help your organization, please contact us.
How it works
The basic structure of Jenbacher CHP systems includes an engine/generator unit and heat exchangers that make use of waste heat. A wide range of heat sources—from engine cooling water and oil to an air/fuel gas mixture and exhaust gas—is configured to maximize the benefit to each individual customer.
Cogeneration systems can be supplemented with a boiler system for bridging peak heat demand periods. An increase in system operating time and efficiency is made possible by the connection of a heat storage medium.
Power plant electrical switch and control systems distribute electricity and manage the engine, while hydraulic equipment ensures heat distribution. Generated power is used by a facility or fed into the public power grid.
The thermal energy can be used to generate heating water and steam production as well as for various types of process heat.
Gas engine cogeneration systems also are used for CO2 fertilization in greenhouses and trigeneration systems (combined generation
Features & Benefits
» Cogeneration systems generate both heat and power
» Jenbacher CHP systems use waste heat from various sources to increase plant efficiency by up to 90 percent
» Cogeneration achieves 40 percent energy savings vs. separate power and heat generation equipment
» Reduces or eliminates transportation and distribution losses
» Addition of boiler system or other heat storage medium further increases operating time and efficiency
» Generated power is used by an individual facility or fed into a public power grid
» Thermal energy can be used to generate heating water and steam production, as well as for various types of process heat
» Cogeneration systems also can be used for CO2 fertilization in greenhouses and trigeneration systems.
CHP Delivers Stable Power Supply for Industry
Utilizing the local natural gas supply network gas engine-based cogeneration systems provide a stable supply of electrical power that, if needed, can be isolated from the local electricity grid. The heat produced by the engine can be recovered either as hot water or as steam for use in the industrial facility. In addition, if there is a local need for cooling power, the heat can be fed into an absorption chiller providing a source of cold water. This cold water can in turn be used to support a refrigeration or air conditioning system. Systems providing electricity, heat and cooling are called trigeneration plants. This can be taken one step further for industrial users that require carbon dioxide. Carbon dioxide can be recovered and scrubbed from the engine exhaust to the highest standards. There are various applications for this carbon dioxide including ones in the food and drinks industry or in greenhouses for the promotion of growth in plants.
CHP Improves Environmental Performance
Natural gas has the lowest levels of carbon dioxide production and is the cleanest of all the fossil fuels. Jenbacher gas engines generate electricity at high efficiency making the greatest use of the fuel source. The utilization of cogeneration for embedded generation helps minimize losses of electricity associated with its transmission from centralized power plants. With the addition of carbon dioxide recovery systems carbon dioxide can be sequestered in plants or utilized in manufacturing processes helping provide the highest levels of environmental performance.
CHP has Varied Industrial Applications
Cogeneration system systems can be successfully applied to a range of industrial applications including:
» Textiles
» Food processing
» Ceramics
» Construction
» Dyes & chemicals
» Mining
» Oil & gas
» Packaging
» Paper
» Pharmaceuticals
» Rubber
» Steel
To find out more about how gas engine based combined heat and power can help your organization, please contact us.
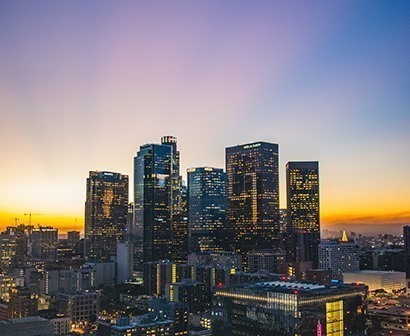